The main reference standards for the design of this system
GB/T 35428-2017 National Standard - Environmental Control Requirements for Negative Pressure Isolation Wards in Hospitals
Environmental requirements for infection control in negative pressure isolation wards of landmark hospitals in Beijing
System Description:
This system consists of: negative pressure chamber, transition room, equipment room, and bathroom (option). The new air treatment and disinfection system is integrated into the system.
Negative pressure chamber, transition room, and bathroom (options)
The negative pressure chamber, transition room, bathroom (optional), and equipment room are arranged inside a complete negative pressure isolation chamber. The warehouse board is insulated with polyurethane.
Technical parameters:
Technical parameters |
numerical value |
Polyurethane thickness (mm) |
100 |
The outer plate is made of color steel plate (mm) |
15 |
The inner plate is made of stainless steel (304) (mm) |
1 |
The floor is made of patterned stainless steel (304) plate (mm) |
3 |
All stainless steel storage plates are welded.
Negative pressure chamber/laboratory:
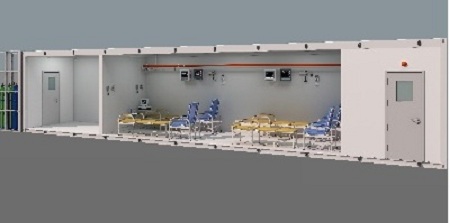
6 (length) * 2.2 (width) * 2.4 (height), can meet the layout requirements of four beds
Transition period:
2 (length) * 1.2 (width) * 2.4 (height), outer single door, inner double door
Including air shower section, circulating air volume of 400m3/h, 6 nozzles
Toilet (option):
1.2 (Depth) * 1.2 (Width) * 2.4 (Height)
The bathroom should be equipped with a special negative pressure collection box for pollutants and a small centralized treatment device.
Brand new air treatment and disinfection system
Fresh air enters from the intake port and passes through the G4 primary filter before entering the ozone disinfection area. Ozone is supplied by an ozone generator. When disinfection is required, evacuate any personnel in the warehouse. Ozone enters the fresh air system through this area and disinfects the entire air system and ward. This disinfection is only carried out at designated times, and ozone is not activated at other times.
The fresh air enters the fresh air treatment cabinet through the ozone disinfection area, and the temperature and humidity required for the outlet are adjusted. At the same time, the variable frequency fan can adjust the supply air volume according to the needs. The fresh air with adjusted temperature and humidity enters the distribution pipeline through the F9 medium efficiency filter, and is sent to the transition room, negative pressure, and bathroom respectively. The air volume of each room is distributed through the air volume control valve to meet the standard requirements.
An H11 high-efficiency filter is installed at the end of the pipeline, and the filtered fresh air enters each room. The air volume entering the room is distributed according to the specified ventilation rate. The position and size of each air outlet shall comply with the standard requirements. There are three air supply ports in the negative pressure chamber, two on both sides and one at the rear of the negative pressure chamber. Low wind speed air supply, 0.15m/s, can achieve a better airflow organization for personnel in the chamber, and the air supply noise is relatively low. The air supply outlet has double-layer louvers that can assist in adjusting the direction of airflow.
Fresh air entering requires cooling and heating, mixing with the air in the room to achieve the desired temperature and humidity. The exhaust gas in the room is sucked in by the exhaust fan from various return air outlets, forming negative pressure. The differential pressure between the transition chamber and the environment is maintained at -5Pa, the negative pressure chamber and the transition chamber are also maintained at -5Pa, and the bathroom (option) and the negative pressure chamber are also maintained at -5Pa. The differential pressure of each part is adjusted by the exhaust electric valve, which can meet the differential pressure requirements of the negative pressure chamber.
Each return air outlet is equipped with a primary filter G4, which filters out dust from the exhaust gas and enters the return air treatment cabinet through the pipeline. The first level of the cabinet is the ozone disinfection section, where the incoming exhaust gas is first subjected to ozone disinfection. Ozone disinfection can be carried out in stages or continuously. After ozone disinfection, it enters the ultraviolet disinfection zone, where 250nm wavelength ultraviolet light disinfects and sterilizes the exhaust gas, achieving the best disinfection effect. Subsequently, the exhaust gas passes through the H14 ultra-high efficiency filter, with a filtration efficiency of 99.997%. Microorganisms that have not been killed by high-efficiency filters will enter the ultraviolet disinfection section to carry out the final killing of viruses.
The disinfected exhaust gas enters the total heat exchanger, where the residual heat and moisture are exchanged for fresh air, and then enters the exhaust gas discharge outlet. Waste gas can be transported through pipelines to the discharge location. The exhaust outlet is equipped with a check valve to prevent air from flowing back into the negative pressure chamber.
automatic control system
This system adopts Siemens' latest generation PLC, S7 1200 as the controller. The PLC with Ethernet interconnection function collects signals from all sensors and intelligently drives various actuators to achieve high-precision automation operation; The operating interface of this system consists of an operation screen and a computer.
If any single component fails, there will be a fault prompt, and the operator can quickly locate the faulty component and troubleshoot according to the prompt; The system will classify and display the type of fault based on its severity, and take different response measures.
Computers can store more and more detailed historical data. And the computer can display dynamic images, and the operator can grasp the operating status of the entire system at a glance based on the vivid dynamic images.
The operator's level is strictly controlled, and only the highest level of authorization can manually operate all executing components of the system;
System technical data
performance category |
performance parameter |
Parameter error |
Temperature setting range (℃) |
20—30 |
±1 |
Humidity range (%) |
40-60 |
±5% |
Total fresh air volume (m ³/h) |
450 |
Variable frequency adjustable |
Total return air (m ³/h) |
510 |
Variable frequency adjustable |
Differential pressure between rooms (pa) |
5(When closing the door) |
±1 |
Fresh air can be taken outdoors or from other suitable locations.
System schematic diagram
Contact: Wang Chaofeng (13701191584) Zhao Jiangshun (18600466869)